In the intricate world of precision engineering, XL Precision Technologies, a UK-based manufacturer, has undergone a remarkable evolution. What began as a family business has now transformed into an established multinational enterprise, boasting a second factory in the US and global sales teams, with ambitious plans for further expansion.
Originally engaged in industries as diverse as oil and gas, aerospace, Formula One, and nuclear marine, XL Precision Technologies found its niche in the precision-engineered medical device components market. In this dynamic field, marked by constant innovation, the company now offers customers direct collaboration with on-site design teams, expediting the journey from component design through testing and clinical trials to production.
Maintaining a high-quality inspection protocol whilst improving cost and time effectiveness is the challenge.
Medical device inspection is critical in ensuring the safety and effectiveness of medical equipment: meeting regulatory standards, ensuring consistency and identifying defects. Maintaining a high-quality inspection protocol whilst improving cost and time effectiveness is the challenge facing businesses in this industry and has been no different for XL Precision Technologies.
As existing owners of Mantis Classic [now Mantis 3rd Gen] and Lynx EVO, their first action was to invite Vision Engineering and alternative providers to demonstrate their latest technology and product line-ups.
How do they consistently meet regulations?
Vision Engineering’s EVO Cam II was initially installed in the electrical discharge machining (EDM) department, serving as a valuable visualisation tool. The quality and flexibility of the magnification, the convenience of the HD display output and the consistency that could be achieved across multiple users were essential features that made the EVO Cam II the perfect balance between quality and cost-effectiveness.
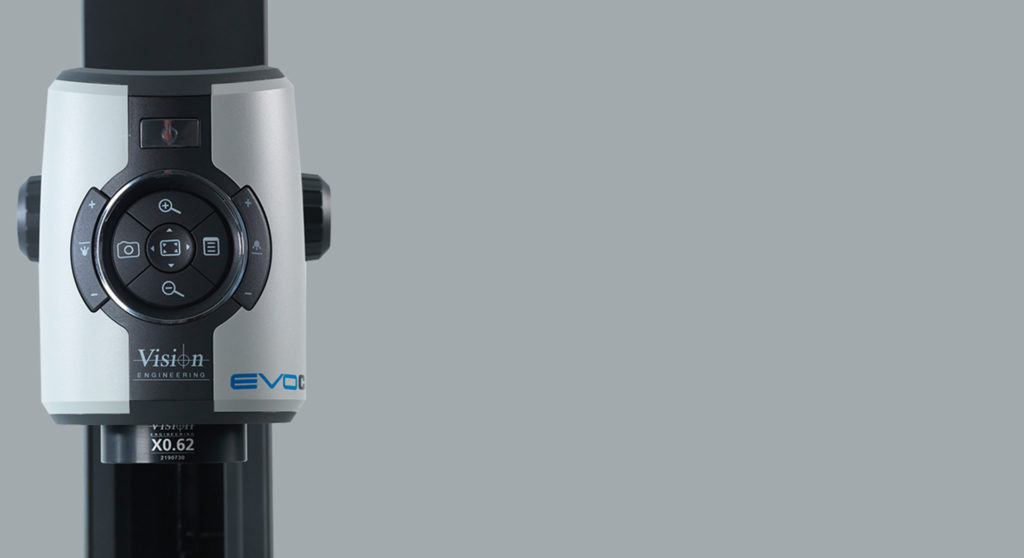
The impact of this product didn’t go unnoticed within the working environment leading to further placements of the EVO Cam II in the laser department, the tool room, and the inspection department.
For XL Precision Technologies, an added bonus was that as they transitioned to newer equipment, Vision Engineering serviced the original units to such a high standard that they were reintegrated into the workflow further enhancing their production process.
In 2023, the company made a further acquisition of a VE Cam with a screen to be integrated into the standard operating procedure (SOP) for a specific product.
On a day-to-day basis on the shop floor, XL Precision Technologies has witnessed a notable transformation.
After the initial challenge of ‘too many faults’ being identified due to operators using magnification levels beyond specification, customised pre-sets have proved invaluable. Overall, the adoption of the Vision Engineering solutions linked to HD screens has simplified the process of identifying and sharing specific issues.
The result – a remarkable 65% decrease in internal rejects.
Unsurprisingly, Vision Engineering products are the de-facto replacement for more budget-friendly but less effective equipment being phased out of the business.
XL Precision Technologies is now looking to strengthen ties by extending its range of Vision Engineering solutions into metrology systems. It is a collaborative approach recognising the importance of finding the optimal solution for their specific product requirements.
For XL Precision Technologies, the investment in Vision Engineering equipment wasn’t just about streamlining processes; it also translated into a positive financial impact. Their advice for potential customers echoes this sentiment:
“Dive into the expertise of Vision Engineering, get hands-on with the product, and chances are, you won’t be let down by the features or the price points.”